Manufacturing Process of Titanium Alloy Valve Parts (Cutting, Drilling and Tool Design)
Titanium and titanium alloys are not only important structural materials for the manufacture of spacecraft such as airplanes and rockets. And it is increasingly used in mechanical engineering, marine engineering, bioengineering and chemical engineering. For example, in the manufacture of valves, stainless steel valves and titanium valves are used in acidic media at the same time. Titanium valves have a better service life.
Adding alloying elements to titanium to form titanium alloy, its strength is significantly improved. σb can be increased from 350 to 700 MPa to 1200 MPa, so the significance of industrial application of titanium alloy is more important. Titanium alloys are generally classified into α-titanium alloy (represented by TA), β-titanium alloy, and (α+β) titanium alloy (represented by TC) according to the structure in use. Commonly used in the three titanium alloys are the α titanium alloy and the (α + β) titanium alloy. Due to the poor machinability of titanium alloys, it brings many difficulties to practical applications. Starting from the relative machinability of titanium alloy, Kangding Company puts forward practical cutting tools based on years of production experience, which can be used as reference for readers.
If the machinability of No. 45 steel is taken as the standard, the machinability of the titanium alloy is about 20 to 40%, and the machinability is inferior to that of stainless steel, but slightly better than that of the superalloy. In the titanium alloy, the machinability of the β-type titanium alloy, the α+β-type titanium alloy and the α-type titanium alloy is gradually improved, and the pure titanium has the best machinability. That is, in general, the higher the hardness of the material, the more alloying elements are added, the worse the machinability of the material. When processing titanium alloys, if the hardness of the material is less than HB 300, a strong sticking phenomenon will occur, and when the hardness is greater than HB370, processing is extremely difficult. Therefore, it is preferable to make the hardness of the titanium alloy material between HB and 370.
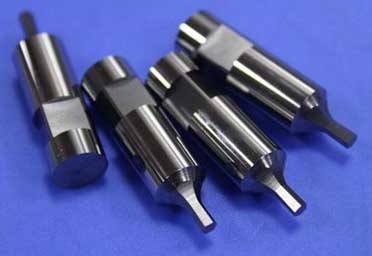
When turning TC4 with YG6X turning tool (hardness is HB320-360), ap=1mm and f=0.1mm/r, the optimum cutting speed is 60mm/min. On this basis, the cutting speed under different tool-feeding and cutting depth is shown in Table 3.
Adding alloying elements to titanium to form titanium alloy, its strength is significantly improved. σb can be increased from 350 to 700 MPa to 1200 MPa, so the significance of industrial application of titanium alloy is more important. Titanium alloys are generally classified into α-titanium alloy (represented by TA), β-titanium alloy, and (α+β) titanium alloy (represented by TC) according to the structure in use. Commonly used in the three titanium alloys are the α titanium alloy and the (α + β) titanium alloy. Due to the poor machinability of titanium alloys, it brings many difficulties to practical applications. Starting from the relative machinability of titanium alloy, Kangding Company puts forward practical cutting tools based on years of production experience, which can be used as reference for readers.
If the machinability of No. 45 steel is taken as the standard, the machinability of the titanium alloy is about 20 to 40%, and the machinability is inferior to that of stainless steel, but slightly better than that of the superalloy. In the titanium alloy, the machinability of the β-type titanium alloy, the α+β-type titanium alloy and the α-type titanium alloy is gradually improved, and the pure titanium has the best machinability. That is, in general, the higher the hardness of the material, the more alloying elements are added, the worse the machinability of the material. When processing titanium alloys, if the hardness of the material is less than HB 300, a strong sticking phenomenon will occur, and when the hardness is greater than HB370, processing is extremely difficult. Therefore, it is preferable to make the hardness of the titanium alloy material between HB and 370.
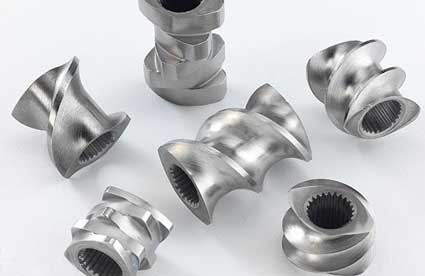
Study on Relative Machinability Cutting Conditions of Titanium Alloy
YT cemented carbide blades are not suitable for processing titanium alloys.
because:
①YT cemented carbide blades contain titanium, which can affinity with the processed titanium alloy and stick off the tip of the tool.
②When turning titanium alloy, the contact between turning tool and chips is much smaller than when turning steel, and the unit cutting tool acting on the contact area of turning tool is larger. Because the YT carbide blade is brittle, it is easy to crack.
In general, YG blades are used to process titanium alloys in production, although their wear resistance is poor. YG8 blade is usually used for rough turning and intermittent turning, YG3 blade for finish turning and continuous turning, and YG6X blade for general turning.
Practice has proved that the effect of tantalum-containing cemented carbide YA6 (which belongs to fine tungsten-cobalt cemented carbide) is better. Due to the addition of a small amount of rare elements, the wear resistance of the blade is improved. Instead of the original YG6X, the bending strength and hardness are also higher than that of the YG6X.
High vanadium high speed steel (W12Cr4V4Mo) and high cobalt high speed steel (W2Mo9Cr4VCo8) can be used in low speed cutting or cutting complex titanium alloy profiles. They are the best tool materials for processing titanium alloys, but because of their low cobalt resources and high cost, they should be used as little as possible to protect scarce resources and reduce costs.
because:
①YT cemented carbide blades contain titanium, which can affinity with the processed titanium alloy and stick off the tip of the tool.
②When turning titanium alloy, the contact between turning tool and chips is much smaller than when turning steel, and the unit cutting tool acting on the contact area of turning tool is larger. Because the YT carbide blade is brittle, it is easy to crack.
In general, YG blades are used to process titanium alloys in production, although their wear resistance is poor. YG8 blade is usually used for rough turning and intermittent turning, YG3 blade for finish turning and continuous turning, and YG6X blade for general turning.
Practice has proved that the effect of tantalum-containing cemented carbide YA6 (which belongs to fine tungsten-cobalt cemented carbide) is better. Due to the addition of a small amount of rare elements, the wear resistance of the blade is improved. Instead of the original YG6X, the bending strength and hardness are also higher than that of the YG6X.
High vanadium high speed steel (W12Cr4V4Mo) and high cobalt high speed steel (W2Mo9Cr4VCo8) can be used in low speed cutting or cutting complex titanium alloy profiles. They are the best tool materials for processing titanium alloys, but because of their low cobalt resources and high cost, they should be used as little as possible to protect scarce resources and reduce costs.
Tool geometry angle
When cutting titanium alloy, the turning angle α0 of the turning tool is the most sensitive of all the tool parameters, because the metal elastic recovery under the cutting layer is large and the processing hardness is large. Generally, large rear angle can make the edge easy to cut into the metal layer and reduce the wear of the flank, but if the rear angle is too small (less than 15 degrees), metal adhesion will occur. If the rear angle is too large, the tool will be weakened and the blade will be fragmented easily. Therefore, most cutting tools for cutting titanium alloys use a 15° relief angle. From the perspective of tool durability, α0 is less than or greater than 15°, which will reduce the durability of the turning tool. In addition, the turning edge with α0 of 15° is sharper and can reduce the cutting temperature.
Since the titanium alloy forms a hard and brittle compound with oxygen, hydrogen, nitrogen, etc. in the air during the cutting process, causing tool wear (mainly on the rake face of the turning tool), a small value front angle should be used; In addition, the plasticity of the titanium alloy is low, and the contact area between the chip and the rake face is small, and a small value of the rake angle should also be used for this purpose. By doing so, the contact area between chip and rake face can be increased, so that cutting heat and cutting pressure can not be too concentrated near the edge. It is not only conducive to heat dissipation, but also strengthens the cutting edge and avoids cutting edge collapse due to the concentration of cutting force. Therefore, when a (α+β) titanium alloy is processed with a cemented carbide tool. Take the rake angle γ0=5° and grind the chamfer f (width 0.05~0.1mm), γf=0°~10°, the tool tip is ground into r=0.5mm small arc, and the blade inclination angle λ=+3 °.
However, the research work shows that the tool has the best durability when the front angle of the turning tool is in the range of 28° to 30°. Increasing the radius of tool tip arc can also reduce tool collapse.
General geometry of turning titanium alloy external turning tools: Chamfering = 0.3 to 0.7 mm, γf = 0°, γ0 = 8° to 10°, α0 = 15°, r = 0.5 mm, λ = 0°, κr = 45°, κ'r = 15°.
Since the titanium alloy forms a hard and brittle compound with oxygen, hydrogen, nitrogen, etc. in the air during the cutting process, causing tool wear (mainly on the rake face of the turning tool), a small value front angle should be used; In addition, the plasticity of the titanium alloy is low, and the contact area between the chip and the rake face is small, and a small value of the rake angle should also be used for this purpose. By doing so, the contact area between chip and rake face can be increased, so that cutting heat and cutting pressure can not be too concentrated near the edge. It is not only conducive to heat dissipation, but also strengthens the cutting edge and avoids cutting edge collapse due to the concentration of cutting force. Therefore, when a (α+β) titanium alloy is processed with a cemented carbide tool. Take the rake angle γ0=5° and grind the chamfer f (width 0.05~0.1mm), γf=0°~10°, the tool tip is ground into r=0.5mm small arc, and the blade inclination angle λ=+3 °.
However, the research work shows that the tool has the best durability when the front angle of the turning tool is in the range of 28° to 30°. Increasing the radius of tool tip arc can also reduce tool collapse.
General geometry of turning titanium alloy external turning tools: Chamfering = 0.3 to 0.7 mm, γf = 0°, γ0 = 8° to 10°, α0 = 15°, r = 0.5 mm, λ = 0°, κr = 45°, κ'r = 15°.
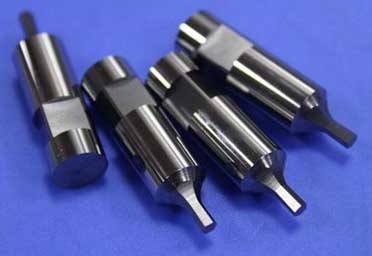
Effect of cutting amount on cutting temperature
When the titanium alloy TA2 is turned by the YG8 insert, the relationship between the change in the cutting parameters and the change in the cutting temperature is known. The cutting temperature t during the machining increases sharply as the cutting speed v increases, and increasing the cutting amount f also increases the cutting temperature t, but the influence thereof is smaller than the effect of increasing the speed. The change in depth of cut has little effect on the cutting speed.
The high cutting speed during machining causes the cutting tool to wear sharply. Further, the titanium alloy has the ability to absorb oxygen and hydrogen from the surrounding atmosphere, resulting in so-called "alphalation of the structure" and strengthening the machined surface.
The cutting temperature is usually maintained at around 800 °C when the cutting speed and the amount of cutting are selected. That is, when the amount of the cutter f is f.11 to 0.35 mm/r, the cutting speed v=40 to 60 m/min is taken.
The high cutting speed during machining causes the cutting tool to wear sharply. Further, the titanium alloy has the ability to absorb oxygen and hydrogen from the surrounding atmosphere, resulting in so-called "alphalation of the structure" and strengthening the machined surface.
The cutting temperature is usually maintained at around 800 °C when the cutting speed and the amount of cutting are selected. That is, when the amount of the cutter f is f.11 to 0.35 mm/r, the cutting speed v=40 to 60 m/min is taken.
Effect of cutting amount on surface roughness
Titanium alloys are sensitive to stress concentration and can seriously reduce their fatigue strength when scratches or dents occur, so the processing requirements of surface quality of titanium alloy parts are very high.
Cutting tool amount has a great influence on surface quality. From the processing of titanium alloy TC6 (speed v = 40m / min, cutting depth ap = 1mm, after the flank wear h ≤ 0.1mm), the relationship between the cutting tool amount and the surface roughness of the machined surface can be known. In order to obtain a surface roughness Ra1.6μm, the amount of pass f = 0.16mm / r must be selected; If the amount of pass f = 0.25 mm / r, 0.35 mm / r and 0.45 mm / r, respectively, is used, the corresponding machined surface roughness obtained is Ra 3.2 μm, Ra 6.3 μm and Ra 12.5 μm.
When cutting titanium alloy, the surface roughness has nothing to do with cutting speed, and the influence of cutting depth is very small. The surface quality changes within the same surface roughness.
When finishing titanium alloy, in order to obtain the surface roughness of Ra1.6μm, YG type cemented carbide insert should be used. The working surface of the grinding tool is taken as: γf=0°, γ0=10°, α0=15°, r=0.5 mm; The cutting amount is selected as: v=50~70mm/min, f=0.1~0.2mm/r, ap=0.3~1.0mm; After the tool wears behind h, it is ≤0.3mm.
By increasing the radius r of the cutting edge, reducing the amount of the cutting f, reducing the wear of the tool by 0.15 mm, and continuously turning the titanium alloy, the surface roughness of Ra = 1.25 to 0.8 μm can be obtained.
3. Titanium alloy cutting and tool design
3.1 Turning processing
The elastic modulus of titanium alloy is small, such as the elastic modulus of TC4 E=110GPa, which is about half of steel. Therefore, the elastic deformation of the workpiece caused by the cutting force is large, which will reduce the precision of the workpiece, and the rigidity of the machining system is improved for this purpose. The workpiece must be clamped very firmly and the tool moment on the workpiece support point is minimized. The tool must be sharp, otherwise vibration and friction will occur, shortening the tool durability and reducing the accuracy of the workpiece.
When cutting titanium alloy, only in the range of cutting speed of 1-5 mm/min can chip tumors form. Therefore, in general production conditions, when cutting titanium alloys, there will be no chip tumors. The friction coefficient between the workpiece and the tool is not very large, and it is easy to obtain a good surface quality. The use of a cooling lubricant has no effect on improving the microscopic geometry of the titanium alloy surface. The low roughness of machined surface in cutting titanium alloy is due to the absence of chip tumors on the tool.
However, in order to improve cutting conditions, reduce cutting temperatures, increase tool life, and to eliminate the risk of fire, it is necessary to use a large amount of soluble coolant during processing.
Usually there is no ignition and combustion in the processing of titanium alloy parts, but there is ignition and combustion in the micro-cutting process, in order to avoid this danger. should:
1. use a large amount of coolant;
2. timely remove the chips from the machine;
3. equipped with fire extinguishing equipment;
4. Replace the blunt tool in time;
5. Sparks are easily caused by workpiece surface contamination, and cutting speed must be reduced at this time.
6. Compared with thin chips, thick chips are not easy to generate sparks, so it is necessary to increase the cutting volume, which will not make the temperature rise as quickly as cutting speed increases.
Selection criteria for the processing of titanium alloys: A lower cutting speed and a larger amount of cutting should be used from the viewpoint of lowering the cutting temperature. Due to the high cutting temperature, the titanium alloy absorbs oxygen and hydrogen from the atmosphere, causing the surface of the workpiece to be hard and brittle, causing the tool to wear excessively. Therefore, during the processing, the temperature of the tool tip must be kept at a suitable temperature to avoid excessive temperature.
When turning a hard-coated titanium alloy workpiece with a YG8 turning tool under intermittent cutting conditions, the recommended cutting amount is: v=15 to 28 m/min, f=0.25 to 0.35 mm/r, and ap=1 to 3 mm.
When using a YG3 turning tool to finish a titanium alloy workpiece under continuous cutting conditions, the recommended cutting amount is: v = 50 to 70 m/min, f = 0.1 to 0.2 mm/r, and ap = 0.3 to 1 mm.
Table 2 shows the amount of cutting available for turning titanium alloys.
Cutting tool amount has a great influence on surface quality. From the processing of titanium alloy TC6 (speed v = 40m / min, cutting depth ap = 1mm, after the flank wear h ≤ 0.1mm), the relationship between the cutting tool amount and the surface roughness of the machined surface can be known. In order to obtain a surface roughness Ra1.6μm, the amount of pass f = 0.16mm / r must be selected; If the amount of pass f = 0.25 mm / r, 0.35 mm / r and 0.45 mm / r, respectively, is used, the corresponding machined surface roughness obtained is Ra 3.2 μm, Ra 6.3 μm and Ra 12.5 μm.
When cutting titanium alloy, the surface roughness has nothing to do with cutting speed, and the influence of cutting depth is very small. The surface quality changes within the same surface roughness.
When finishing titanium alloy, in order to obtain the surface roughness of Ra1.6μm, YG type cemented carbide insert should be used. The working surface of the grinding tool is taken as: γf=0°, γ0=10°, α0=15°, r=0.5 mm; The cutting amount is selected as: v=50~70mm/min, f=0.1~0.2mm/r, ap=0.3~1.0mm; After the tool wears behind h, it is ≤0.3mm.
By increasing the radius r of the cutting edge, reducing the amount of the cutting f, reducing the wear of the tool by 0.15 mm, and continuously turning the titanium alloy, the surface roughness of Ra = 1.25 to 0.8 μm can be obtained.
3. Titanium alloy cutting and tool design
3.1 Turning processing
The elastic modulus of titanium alloy is small, such as the elastic modulus of TC4 E=110GPa, which is about half of steel. Therefore, the elastic deformation of the workpiece caused by the cutting force is large, which will reduce the precision of the workpiece, and the rigidity of the machining system is improved for this purpose. The workpiece must be clamped very firmly and the tool moment on the workpiece support point is minimized. The tool must be sharp, otherwise vibration and friction will occur, shortening the tool durability and reducing the accuracy of the workpiece.
When cutting titanium alloy, only in the range of cutting speed of 1-5 mm/min can chip tumors form. Therefore, in general production conditions, when cutting titanium alloys, there will be no chip tumors. The friction coefficient between the workpiece and the tool is not very large, and it is easy to obtain a good surface quality. The use of a cooling lubricant has no effect on improving the microscopic geometry of the titanium alloy surface. The low roughness of machined surface in cutting titanium alloy is due to the absence of chip tumors on the tool.
However, in order to improve cutting conditions, reduce cutting temperatures, increase tool life, and to eliminate the risk of fire, it is necessary to use a large amount of soluble coolant during processing.
Usually there is no ignition and combustion in the processing of titanium alloy parts, but there is ignition and combustion in the micro-cutting process, in order to avoid this danger. should:
1. use a large amount of coolant;
2. timely remove the chips from the machine;
3. equipped with fire extinguishing equipment;
4. Replace the blunt tool in time;
5. Sparks are easily caused by workpiece surface contamination, and cutting speed must be reduced at this time.
6. Compared with thin chips, thick chips are not easy to generate sparks, so it is necessary to increase the cutting volume, which will not make the temperature rise as quickly as cutting speed increases.
Selection criteria for the processing of titanium alloys: A lower cutting speed and a larger amount of cutting should be used from the viewpoint of lowering the cutting temperature. Due to the high cutting temperature, the titanium alloy absorbs oxygen and hydrogen from the atmosphere, causing the surface of the workpiece to be hard and brittle, causing the tool to wear excessively. Therefore, during the processing, the temperature of the tool tip must be kept at a suitable temperature to avoid excessive temperature.
When turning a hard-coated titanium alloy workpiece with a YG8 turning tool under intermittent cutting conditions, the recommended cutting amount is: v=15 to 28 m/min, f=0.25 to 0.35 mm/r, and ap=1 to 3 mm.
When using a YG3 turning tool to finish a titanium alloy workpiece under continuous cutting conditions, the recommended cutting amount is: v = 50 to 70 m/min, f = 0.1 to 0.2 mm/r, and ap = 0.3 to 1 mm.
Table 2 shows the amount of cutting available for turning titanium alloys.
Table 2. Cutting amount when turning titanium alloy
Process Properties - Titanium Alloy Material - Hardness - Cutting allowance (mm) - Cutting speed (mm/min) - Feeding amount (mm/r)
Waste turning-TA1~7, TC1~2-soft->oxide thickness -18~36-0.1~0.25
Waste turning-TA8, TC3~8-中->scale thickness -12~27-0.08~0.15
Waste turning-TC9~10, TB1~2-hard->scale thickness-7.2~18-0.06~0.12
Rough turning-TA1~7, TC1~2-soft->2-30~54-0.2~0.4
Rough turning-TA8,TC3~8-中->2-24~54-0.15~0.3
Rough turning-TC9~10, TB1~2-hard->2-15~30-0.1~0.2
Rough turning-TA1~7, TC1~2-soft-0.07~0.75-37.5~60-0.07~0.15
Rough turning-TA8,TC3~8-中-0.07~0.75-30~48-0.07~0.12
Rough turning-TC9~10, TB1~2-hard-0.07~0.75-18~36-0.05~0.12
Waste turning-TA1~7, TC1~2-soft->oxide thickness -18~36-0.1~0.25
Waste turning-TA8, TC3~8-中->scale thickness -12~27-0.08~0.15
Waste turning-TC9~10, TB1~2-hard->scale thickness-7.2~18-0.06~0.12
Rough turning-TA1~7, TC1~2-soft->2-30~54-0.2~0.4
Rough turning-TA8,TC3~8-中->2-24~54-0.15~0.3
Rough turning-TC9~10, TB1~2-hard->2-15~30-0.1~0.2
Rough turning-TA1~7, TC1~2-soft-0.07~0.75-37.5~60-0.07~0.15
Rough turning-TA8,TC3~8-中-0.07~0.75-30~48-0.07~0.12
Rough turning-TC9~10, TB1~2-hard-0.07~0.75-18~36-0.05~0.12
When turning TC4 with YG6X turning tool (hardness is HB320-360), ap=1mm and f=0.1mm/r, the optimum cutting speed is 60mm/min. On this basis, the cutting speed under different tool-feeding and cutting depth is shown in Table 3.
Table 3. Cutting speed of turning titanium alloy TC4
Ap-1mm-2mm-3mm
F(mm/r)-0.1, 0.15, 0.2, 0.3-0.1, 0.15, 0.2, 0.3-0.1, 0.2, 0.3
V(mm/min)-60,52,43,36-49,40,34,28-44,30,26
Typical turning tools for machining titanium alloys have the following characteristics:
1. The blade material is YG6X and YG10HT.
2. The front angle is small, generally γ0=4°~6°, which enhances the strength of the cutter head;
3. has a negative chamfer of f = 0.05 ~ 0.1mm to enhance the strength of the blade;
4.The back angle is large, generally α0=14°~16°, to reduce the friction behind and improve the durability of the tool;
5. Generally, sharp corners or transition edges are not allowed to be ground, and the rounded corners of the grinding edge are r=0.5mm, and the roughing can reach r=1~2mm to enhance the strength of the cutting edge;
6. When finishing or turning thin-walled parts, the main deviation angle of the tool is large, usually 75 ~90.
3.2 Drilling
Titanium alloy drilling is difficult. Burning and drill breakage often occur in the process of drilling. The main reasons are poor grinding of drill bits, untimely debris removal, poor cooling and poor rigidity of process system.
(1) Selection of drill bit: For drills with a diameter greater than 5 mm, it is best to use cemented carbide YG8 as the tool material; When processing holes smaller than 5mm, high-speed steel drill bits (such as M42 or B201) with hardness greater than 63HRC can be used; When the hole depth is less than twice the diameter, the inclined groove (short type) bit is used. When the hole depth is more than twice the diameter, a twist drill is used. Geometric parameters of the drill bit: λ = 0 ° ~ 3 °, α c = 13 ° ~ 15 °, 2φ = 120 ° ~ 130 °.
In order to facilitate the formation of chips, reduce friction and improve the cutting ability of the drill bit. The width of the guide edge band can be reduced to 0.1 0.3 mm and the cross edge can be grinded to 0.1D according to the diameter of the drill bit. And double sharpening apex angle 2φ=130°~140°, 2φ=70°~80°. Table 4 lists the geometric parameters of the double-point drill bit.
F(mm/r)-0.1, 0.15, 0.2, 0.3-0.1, 0.15, 0.2, 0.3-0.1, 0.2, 0.3
V(mm/min)-60,52,43,36-49,40,34,28-44,30,26
Typical turning tools for machining titanium alloys have the following characteristics:
1. The blade material is YG6X and YG10HT.
2. The front angle is small, generally γ0=4°~6°, which enhances the strength of the cutter head;
3. has a negative chamfer of f = 0.05 ~ 0.1mm to enhance the strength of the blade;
4.The back angle is large, generally α0=14°~16°, to reduce the friction behind and improve the durability of the tool;
5. Generally, sharp corners or transition edges are not allowed to be ground, and the rounded corners of the grinding edge are r=0.5mm, and the roughing can reach r=1~2mm to enhance the strength of the cutting edge;
6. When finishing or turning thin-walled parts, the main deviation angle of the tool is large, usually 75 ~90.
3.2 Drilling
Titanium alloy drilling is difficult. Burning and drill breakage often occur in the process of drilling. The main reasons are poor grinding of drill bits, untimely debris removal, poor cooling and poor rigidity of process system.
(1) Selection of drill bit: For drills with a diameter greater than 5 mm, it is best to use cemented carbide YG8 as the tool material; When processing holes smaller than 5mm, high-speed steel drill bits (such as M42 or B201) with hardness greater than 63HRC can be used; When the hole depth is less than twice the diameter, the inclined groove (short type) bit is used. When the hole depth is more than twice the diameter, a twist drill is used. Geometric parameters of the drill bit: λ = 0 ° ~ 3 °, α c = 13 ° ~ 15 °, 2φ = 120 ° ~ 130 °.
In order to facilitate the formation of chips, reduce friction and improve the cutting ability of the drill bit. The width of the guide edge band can be reduced to 0.1 0.3 mm and the cross edge can be grinded to 0.1D according to the diameter of the drill bit. And double sharpening apex angle 2φ=130°~140°, 2φ=70°~80°. Table 4 lists the geometric parameters of the double-point drill bit.
Table 4. Geometric parameters of double front angle drill bits
Drill diameter (mm) - apex angle 2φ - second apex angle 2φ0 - second front edge relief angle α-b(mm)-c(mm)
>3~6-130°~140°-80°~140°-12°~18°-~1.5-0.4~0.8
>6~10-130°~140°-80°~140°-12°~18°-1.5~2.5-0.6~1
>10~18-125°~140°-80°~140°-12°~18°-2.5~4-0.8~1
>18~30-125°~140°-80°~140°-12°~18°-4~6-1~1.5
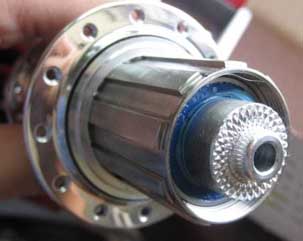
Drill diameter (mm) - apex angle 2φ - second apex angle 2φ0 - second front edge relief angle α-b(mm)-c(mm)
>3~6-130°~140°-80°~140°-12°~18°-~1.5-0.4~0.8
>6~10-130°~140°-80°~140°-12°~18°-1.5~2.5-0.6~1
>10~18-125°~140°-80°~140°-12°~18°-2.5~4-0.8~1
>18~30-125°~140°-80°~140°-12°~18°-4~6-1~1.5
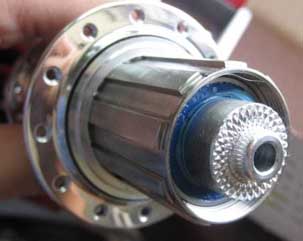